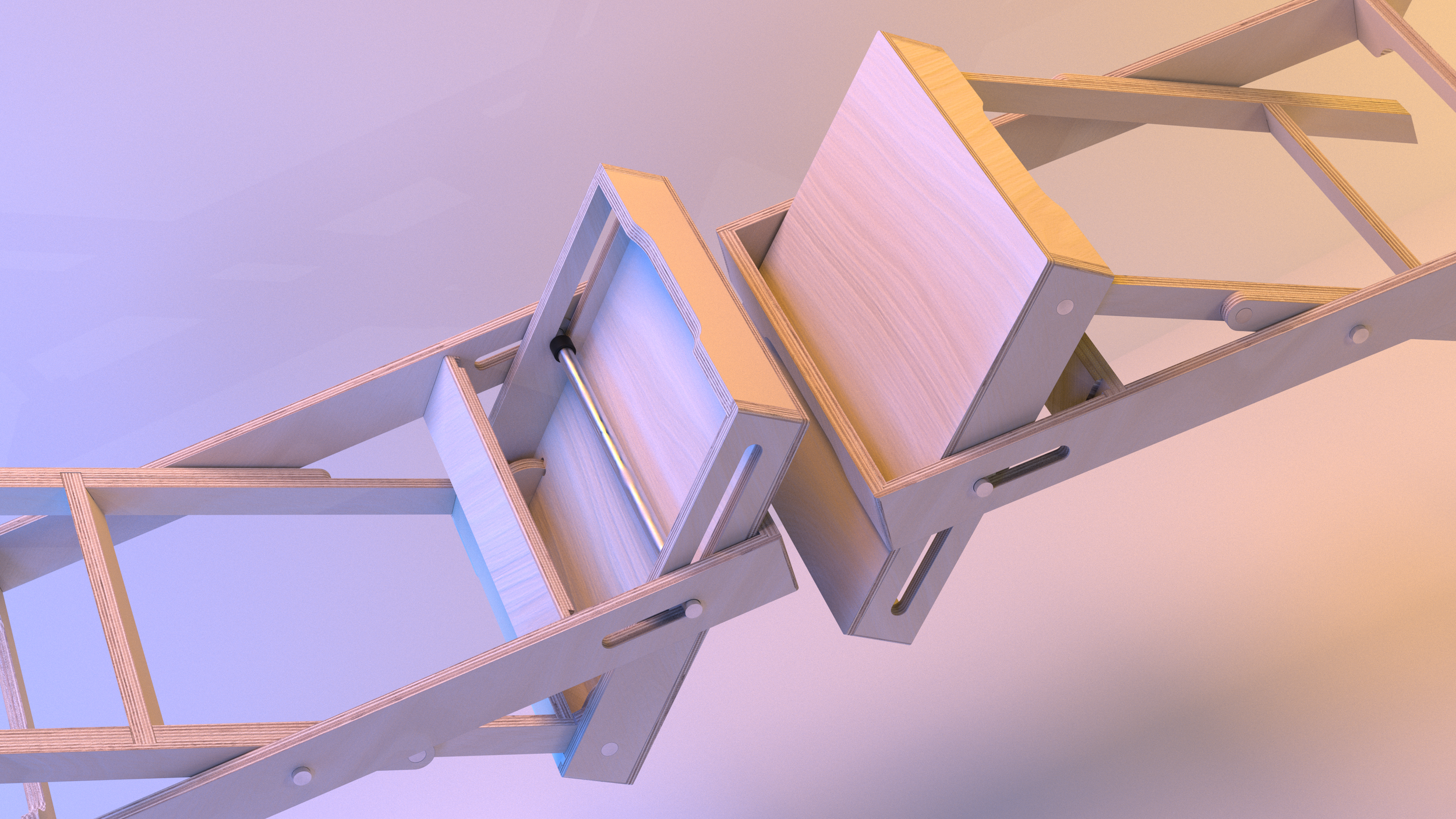
MOGUS.POKUS
a space conscious seating solution
DVC
5 WEEK PROJECT
2025
CAD, CNC, MODEL MAKING, PROTOTYPING
FUSION, VCARVE, SHOPBOT, KEYSHOT
Tiny homes have likewise seen a growing trend in popularity.
The tiny home of Environment conservationist Maya Higa, delivered to her non-profit animal sanctuary, Alveus.
Trends in home renting has surged in recent years, driven by a wave of Gen Z approaching their 30s.
Gen Z, the only renter-majority generation, eclipsed 5 million households in 2022 and will become the largest renter demographic by 2030.
Gen Z faces more significant barriers to homeownership than their parents did, including elevated interest rates, a higher cost of living, and a limited supply of quality housing.
(Seippel, T. (2024, March 8). Why generation Z is leaning into the renting lifestyle.)
US Census Bureau
lack of space and difficulties around accessible storage.
Moving furniture is an obnoxious and stressful endevour.
Socio-economic volatility and growing environmental/climate concerns.
Space efficient and practical living space solutions (furniture, appliances, etc) for small, modular or mobile housing.
Market Opportunity:
The top three reasons for downsizing to a tiny home are financial freedom, simplicity, and mobility.
In a survey conducted by U.S. News & World Report, 60% of Americans would consider living in a tiny home.
In recent years, there has been an increase in the number of cities that have changed their zoning laws to allow for more flexible housing options such as Tiny Homes. These cities include Detroit, Minneapolis, and Portland.
(https://www.homechoicenys.com/blog/tiny-homes-statistics)
EMMA MOGUS
Emma lives in a cozy apartment in the heart of the Silicon Valley. A reliable host and the life of the party, Emma routinely limit tests the capacity of her apartment. On a few occasions, she’s had to source a set of folding chairs for the evening, only to have to plan the following day around returning them - a headache not unlike a hangover.
As an interior design and furniture nut, she has taken special care in furnishing and staging the apartment.
Senior Battery/Reliability Engineer, 26
“Photography, camping, geeking out about interior design.”
Emma could appreciate an easily deployable, space efficient, and attractive seating solution for her apartment.
Palo Alto, CA
Just so happens to be the perfect candidate for a belated birthday present…
A set of at least 2 chairs.
Wall mounting for stowage.
Includes a mechanical component.
The backbone of the mechanism- the half inch aluminum rod.
GIVEN:
5 week timeline.
4’ x 4’ sheet of plywood.
CNC routing as the primary manufacturing process.
SELF IMPOSED:
IN THE SPIRIT OF
MID-CENTURY MODERN
CONSTRAINTS
OPPORTUNITY FOR GROWTH
One more constraint/personal goal I set for this project: using cardboard and mockups to drive the development of the design. CAD only to bring it to the finish line. Of note, this was my first foray into furniture design.
WARM UP
UNDERSTANDING CARDBOARD
Starting the ID program at the tail end of the Pandemic, the crucial practice of model making seemed to have fallen through the cracks. I wanted this chance to slow down and really play with the cardboard, and get more comfortable with working with my hands.
Manipulating cardboard not only allowed me to understand form in physical space, but also get a better feel for the integrity of certain structures, and how to reinforce them.
TRANSLATING TO PLYWOOD
Building a joint “tower” was incredibly helpful in understanding the limitations of the CNC router. Most importantly, it introduced me to the art of wood joinery.
THINK WHERE YOU WORK
What started as a dimensional layout/ thinking sketch evolved into an exciting render.
I wanted the chair to feel stable to sit on and satisfying to deploy.
I set out on a quest to find material-efficient ways of adding bracing and optimizing the mechanical components of the chair.
STRETCHING LEGS
ft. toothpick + painters tape
I latched on to this idea of a stool with a detail suggesting a low back, but not necessarily function as one.
A very crude mockup, focusing on the general volume and conceptualizing the individual components of the chair. Most importantly, I got a starting point for the mechanism that I had envisioned for this project.
Initially I had envisioned the chair to fold flat for storage, only to then ask, why should it?
Preemptive measuring insured quick reproduction of the mock ups, allowing for quicker iterations.
“EXOSKELETON”
Gravitating towards using the corners of the box to improve rigidity. Triangles…
LOAD DISTRIBUTION
As I am not an engineer, this approach would allow me some grace when designing for the physical demands required of the mechanism.
Finer tolerance out of thinner cardboard for the “underpinnings.”
My biggest concern was longevity of the chair. As such, I figured I needed to find a way in which the chair could support itself through its inherent structure in order to reduce load and wear on the important bits.
Structural components out of corrugated board.
A valuable exercise, but ultimately made me realize the concept was resource heavy and would have been difficult to translate into wood reliably.
She stands proud. After some more massaging of the tolerances and adjusting the range of motion, the model worked surprisingly well and felt stable.
QUARTER SCALE/LASER CUT
Quarter scale in not just the surface area of the material, but its thickness as well.
This was the final step before committing to the real deal.
I had to keep into account that the laser cutter was only limited to through-cuts. I had to modify the joints accordingly.
A polycarb dowel was scavenged and used as the pivot for the slider. To keep it from slipping out, I tightly rolled two strips of sticky notes around the center.
JOINING IT ALL TOGETHER
I couldn’t help myself from freestyling some of the joints.
ON THE OPERATING TABLE
Time was dwindling, with only an evening and a sleepless night left between my cutting the panel on the router and putting it all together for the presentation the following morning.
BUT WAIT…THERE’S ALWAYS MORE.
Stressed and exhausted, I inevitably messed up the toolpath. By some miracle, I had just enough pieces to pull together one chair.
…but not without having to put in an obscene amount of elbow grease. Virtually all pieces had to be corrected manually for fitment. This was my first time improvising with a pull saw and chisel.
Intersecting pockets of variable depths. None of them turned out correct, but two were salvageable.
Straight off the router table.
Nylon washers were used as spacers between the “back” legs and the box to the excess room. I also found some 0.5” automotive hose to secure the rod from the inside.
Following some emergency surgery.
I had bought an aluminum rod as the pivot for the hinge. My goal was to secure them within the chair with a friction fit, in the spirit of easy assembly.
In fact, it was not easy to assemble. I found out that 0.5” bored out by the router did not correlate with the diameter of the extruded piece of aluminum. The holes and slots I had made were significantly undersize, and a lot of time was wasted getting them to size with sandpaper.
The upper brace for the front legs was tucked neatly out of the way in order to avoid visual clutter.
TAKE A SEAT
Leans conveniently up against a wall when folded without the hanger, in a pinch.
The whole set fits on a 48” x 48” sheet of plywood, easy to pack, ship, and assemble.